Lathe machines are a cornerstone of metalworking and manufacturing industries, known for their versatility and precision. Whether you’re a beginner or an experienced machinist, understanding the fundamental turning operations can significantly improve your work quality and efficiency. As an eminent industrial equipment supplier, we provide a number of excellent lathe machines that meet the diversity of the requirements from a variety of industries. In this blog, we’ll take a look at 10 basic turning operations that every machinist ought to know.
1. Straight Turning
Straight turning is one of the most fundamental yet widely used operations on a lathe machine. This operation entails that machining is done on the workpiece surface to give a cylindrical shape. This operation is indispensable for reducing the diameter and bringing a smooth and consistent finish on that diameter.
2. Taper Turning
Taper turning refers to the process of producing straight or exactly conical effects on the workpiece. This has reference where diameters of workpiece decrease on both sides toward a point. This is most important for parts that must fit tightly, such as machine-tool spindles and automotive products. Methods include using a taper attachment, offsetting the tailstock, or adjusting the compound rest.
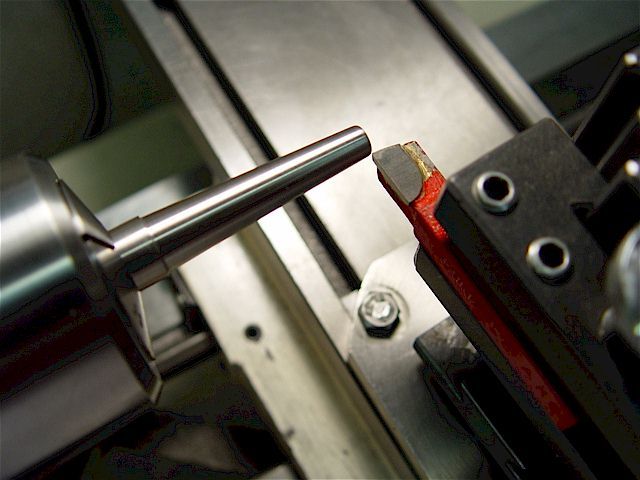
3. Facing
Facing refers to the process of the cutting made flatly perpendicular to the-axis of the workpiece) in rotation. Such operations on a workpiece are used generally to prepare ends of the workpiece for downstream machining or to get it to the required length. A flat face should be made to give an even touch after assembly, which is quite essential for its functioning.
4. Grooving
Grooving is cutting out narrow channels or grooves on the workpiece. This is often applied in creating clearances for retaining rings as well as lightening of the workpiece. Grooving tools are made in practical shapes and sizes to give a perfectly made dimension by machinists.
5. Parting (Cut-Off)
The process of separating a machined component from the stock material is known as parting or cut-off. Using a specialized parting tool, machinists can achieve clean, precise cuts. This operation is critical for producing multiple identical parts from a single workpiece.
6. Thread Cutting
The process of making external or internal screw threads on a workpiece on a lathe machine is referred to as thread-cutting. Manual methods, as well as CNC controls for accurate production, can perform this operation. These threads, though imperceptibly in many cases, are useful for fasteners and bolts and many other members of machines.
7. Knurling
The purpose of knurling is to create a patterned surface on a part, improving its grip. Some of the common applications for this are tool handles and knobs. Knurling tools can come in varieties with different patterns, either straight, diamond, or angled, thus obtaining designs by the operator’s choice.
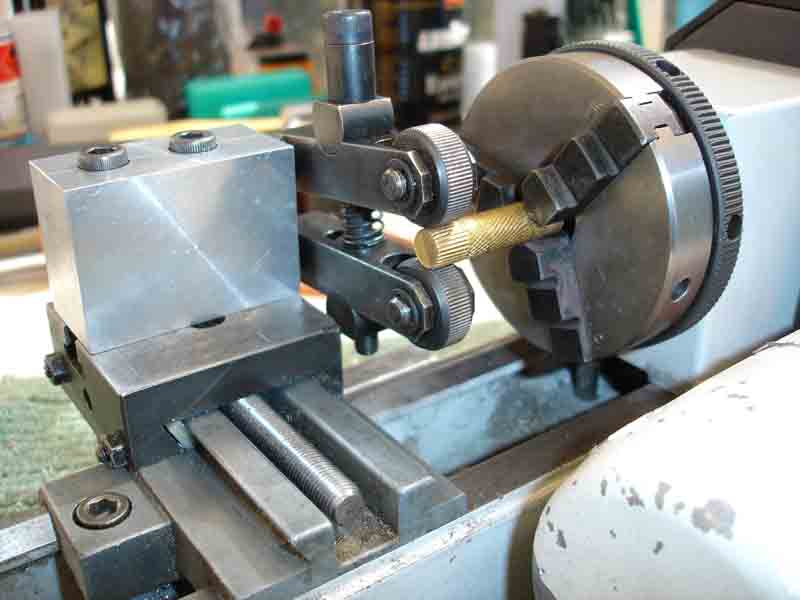
8. Boring
This is the process by which a hole already present on the workpiece is made larger, with precise tolerances and a smooth finish. This operation is critically important to achieve certain tolerances on internal diameters of various components, such as bushings and cylinders. Depending on the particular diameter range on bore size desired, boring bars vary in size.
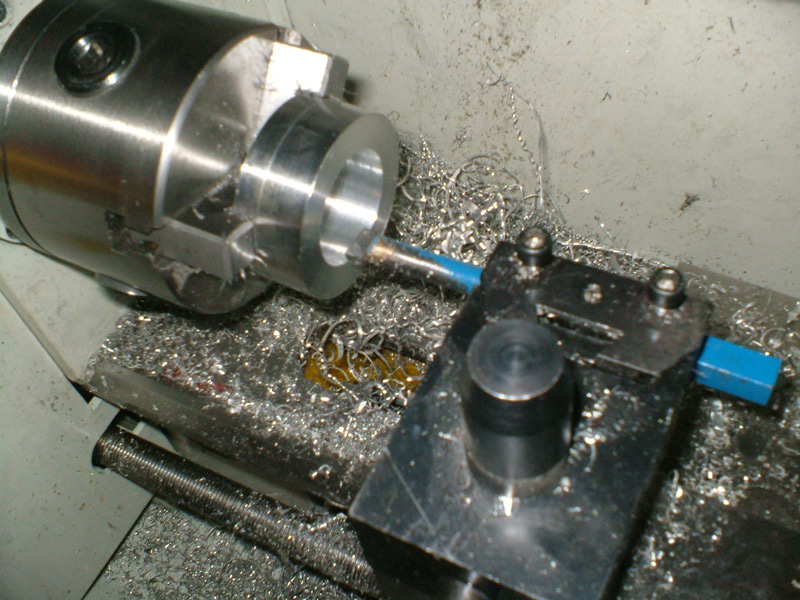
9. Drilling
While typically associated with drill presses, drilling can also be performed on a lathe machine. This process utilizes a stationary drill bit to form holes in a rotating workpiece. Drilling on a lathe allows for greater precision and alignment.
10. Reaming
This is a finishing operation that serves to achieve the desired size and surface finish for a previously drilled hole. It serves to make sure that the holes continue to the required tolerances and remain perfectly round. Reaming tools will cut out a very small amount of material, creating a nice, smooth, round hole.
Why Choose Rockwood Workshop Machines for Your Lathe Machine Needs?
Rockwood Workshop Machines being one of the trustworthy industrial equipment supplier in UAE, offers one of the widest ranges of lathe machine made in accordance to the highest industry standards. Rockwood lathe machines are extremely durable, precise, and efficient, making them perfect for all kinds of turning operations. We provide expert advice on choosing the best equipment for your needs in order to gain the most performance and productivity.
Gaining mastery over these basic lathe machine operations will generally support your machining performance. Quite literally, efficient production of simple and complex components depends on the turning techniques in machining. For those who prioritize reliable and efficient lathe machines, trust the industrial equipment supplier today. Feel free to contact us if you want to explore our products in further detail for assistance with your machining needs.
To read more blogs, click here: How to Choose the Right Punch for Your Hydraulic Punching Machine