Understanding fully the extremes of modern manufacturing, it is clear that industries are constantly updating technologies and techniques for efficiency and accuracy. Of course, some machines are still irreplaceable, despite technological advances. One such example, and the focus of this article, is the hydraulic tapping machine used for heavy-duty threaded applications.
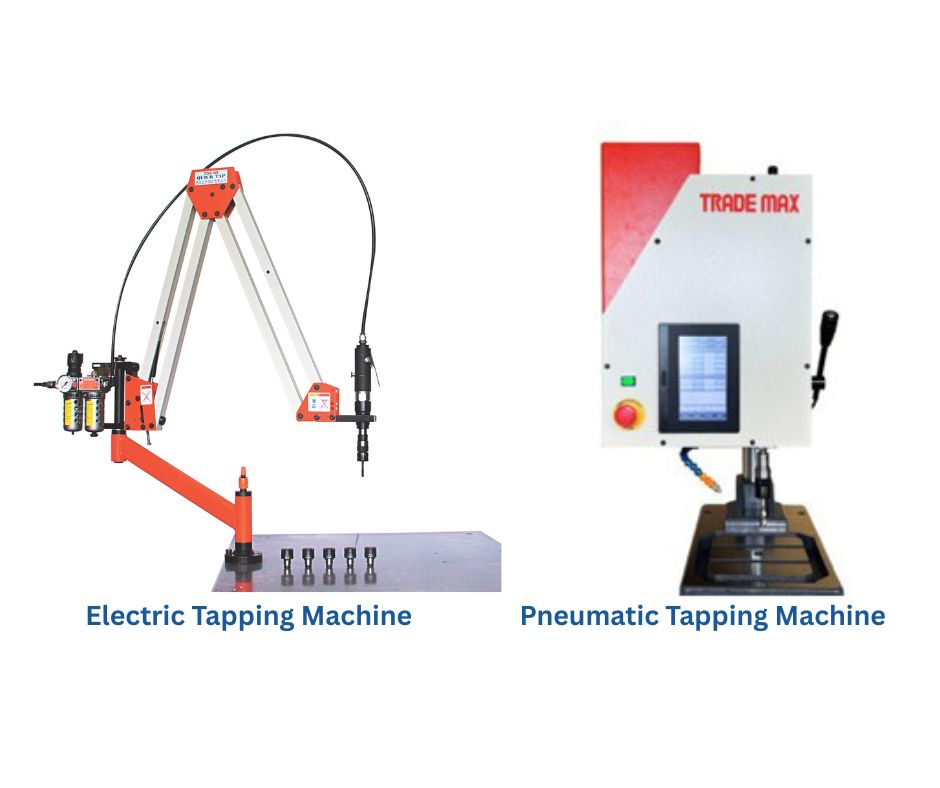
In regions with lower levels of production, electric and pneumatic tapping machines are popular for lighter-duty applications, but hydraulic machines still lead the industry for demanding applications. This machine is still an important part of most factories and is highly recommended by most commercial machinery suppliers.
1. Exceptional Torque Output
Hydraulic tapping machines are known for delivering high, consistent torque, making them ideal for cutting threads into hard materials like cast iron, stainless steel, and titanium.
Heavy-duty threading requires machines built for high stress, without sacrificing quality and tool integrity. Hydraulic systems can produce torque beyond what electric or pneumatic machines can generate, thereby producing a clean and precise thread, even with tough materials.
Many industries, including automotive, shipbuilding, and oil & gas, rely on hydraulic tapping machines to handle large diameter taps with little effort.
2. Precision and Operational Control
When it comes to threading operations, precision is everything. When using a hydraulic tapping machine, the operator has complete control of speed, feed rate, and torque. With a more finely-tuned control system, thread breakouts can be minimized and tool breakage can be mitigated during the process of tapping with a hydraulic machine.
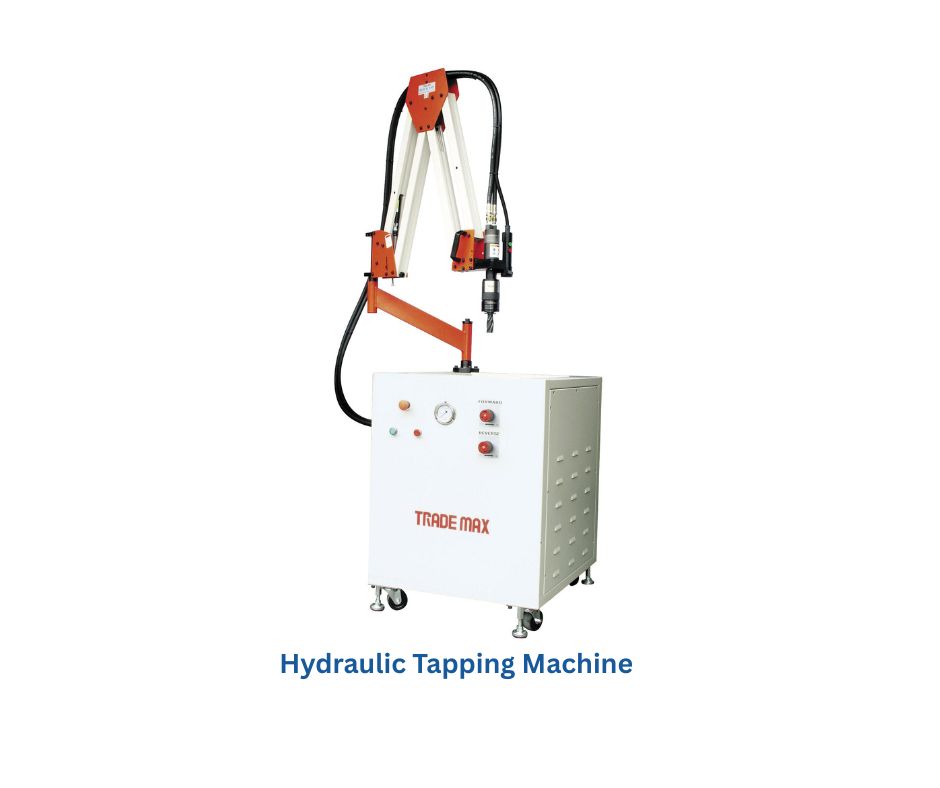
Hydraulic machines will also operate smoothly because there are no abrupt motions, maintaining a steady and consistent quality of threading while extending the life of the tool.
Again, because of the precision compatibility and capabilities of these machines, many industrial equipment suppliers recommend these heavy-duty tapping machines for accuracy and reliable functions.
3. Durability and Reliability
Hydraulic tapping machines are designed for effective and continuous use in difficult situations. Unlike electric motors, which can overheat under heavy loads, a hydraulic system is intrinsically built with large reservoirs of oil to dissipate heat resulting in a lower chance of machine failure.
Hydraulic tapping machines generally have a smaller number of moving parts, meaning lower maintenance and breakdowns over a period of time.
In industries that are aiming to decrease downtime, working with reputable industrial equipment suppliers to source high-quality tapping machines that will provide time savings and long-term value is the best option.
4. Versatile Applications
Hydraulic tapping machines perform extremely well throughout many industries, from aerospace and defense to heavy equipment and oil & gas.
They are designed to accommodate different materials, from soft metals such as aluminum to high-strength alloys.
Many industrial equipment suppliers highlight hydraulic tapping machines as best for tapping operations when deep, large, or precision threading is required.
5. Enhanced Safety Features
The safety features of a hydraulic tapping machine are carefully engineered into its design. Most machines come equipped with torque-limiting mechanisms to avoid over-torquing and have automatic reversing features that prevent damage to threads.
All of these operational safety mechanisms keep operators safer and increase the chances of not breaking a tool. In most heavy-duty applications, hydraulic tapping machines are much safer to use than pneumatic tapping machines.
If you choose to work with reputable industrial equipment suppliers, you are also receiving machines that meet the safety technologies available today.
6. Cost-Effective in the Long Run
Although these machines require a larger initial investment, they tend to deliver greater long-term savings.
Their long-lasting construction, minimal upkeep, and high-level performance reduce operational costs. Additionally, the ability to produce high-quality threads means less scrap and fewer rejected parts, further improving profitability.
Many industrial equipment suppliers recommend hydraulic tapping machines as a smart long-term investment for heavy-duty operations.
7. Proven Track Record
Hydraulic tapping machines have been a staple in industrial settings for decades, thanks to their proven reliability and performance.
Despite advancements in automated systems, experienced machinists still prefer hydraulic tapping machines for large-scale threading tasks where power and precision are critical.
This longstanding reputation keeps them in high demand among industrial equipment suppliers and manufacturers alike.
Final Thoughts
Even as manufacturing technologies evolve, hydraulic tapping machines remain an essential tool for heavy-duty threading. Their unmatched torque, precision, durability, and safety make them ideal for industries requiring reliable and consistent performance.
For manufacturers looking to boost productivity and maintain high-quality standards, investing in hydraulic tapping machines is a practical and strategic decision. Partnering with reputable industrial equipment suppliers like Rockwood Workshop Machines ensures access to top-performing machines that deliver long-term value.
In the world of industrial threading, hydraulic tapping machines continue to prove that some tools simply can’t be replaced.
To read more blogs, click here: Industrial Equipment Import Rules in the UAE: What You Need to Know