Hydraulic punching machines are important tools in the metalworking industry, designed to create precise holes in different materials efficiently. Choosing the right punch for your machine is essential to maintaining quality, improving productivity, and extending the lifespan of both the punch and the machine itself. Whether you are a manufacturer, a fabricator, or a metalworker, selecting the right punch can enhance operations and prevent downtime. This guide will assist you in understanding the different elements involved in selecting the hydraulic punching machined punch in the best possible way.
Using Hydraulic Punching Machines
Hydraulic punching machines utilize hydraulic forcing to push a punch into metal or other materials, producing holes that are clean and accurate. These efficient machines, valued for their ability to work with thick materials, are commonly utilized in the construction, automotive, and metal fabrication industries. When selecting the right punch, performance is observed to be improved. It also assures the durability of the punch along with the machine.
Key Factors in Choosing the Right Punch
1. Material type and thickness matter
Material type and punch thickness go hand-in-hand in selecting your punch. Materials with diverse compositions, including aluminum, stainless steel, and mild steel, have different hardness characteristics. While stainless steel would require a high-strength punch (one made of carbide or coated tool steel), aluminum, being a softer metal, can be processed by using a standard steel punch. Checking material specifications helps you select the appropriate punch, ensuring optimal results.
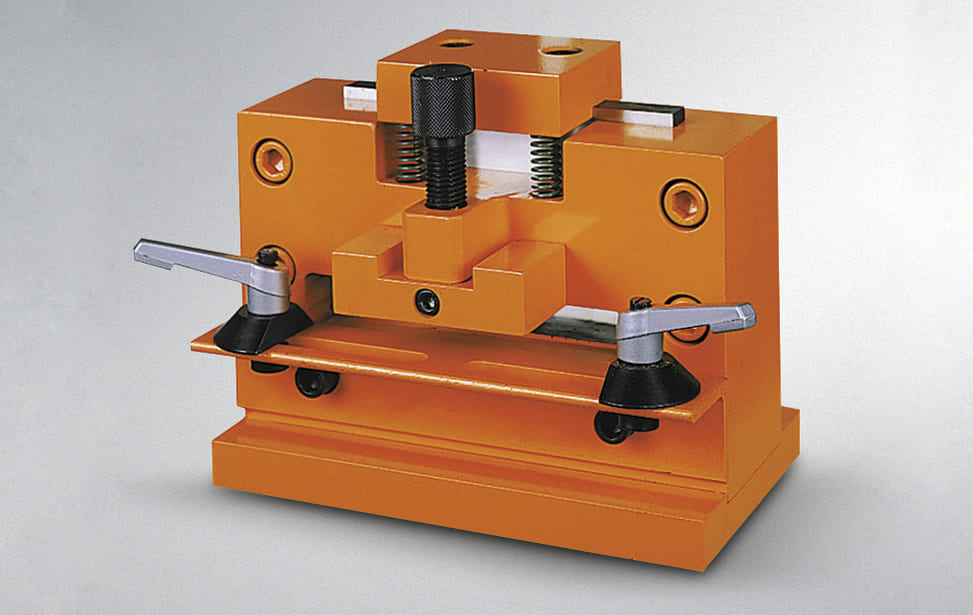
2. Choose the Right Punch Material and Coating
Punches are machined from one of several materials, each having its implications for durability and performance. The most common are:
– High-speed steel (HSS): For moderate-duty uses; it has decent resistance to wear.
– Carbide: Very hard, long-lived; good for punching high-strength metals.
– Tool steels with coatings: Coatings like titanium nitride (TiN) lengthen durability and lower friction, increasing punch lifespan.
With a punch made from the proper material with a protective coating, longevity advantages are assured with a significantly reduced maintenance cost.
3. Select the Appropriate Punch Shape and Size
There are different punches of various shapes and sizes for different hole types, including
– Round: The normal shape used in most jobs.
– Square: Mostly used in electrical and structural jobs.
– Oval and Rectangular: Used in slots and special applications.
– Custom shapes: That are designed for specific industry needs.
Selecting a punch that is correct in size prevents material deformation and gives a clean cut of good quality.
4. Make sure there is proper clearance and alignment for the die.
This is the spacing between the punch and die. The appropriate clearance would help reduce the formation of burrs and protract punch life. The ranges of ideal clearance based on material thickness are mentioned below:
-Less clearance would cause early wear and punch failure.
-More clearance would cause ragged edges and bad hole quality.
Proper alignment of the punch and die is important to guarantee accurate cuts with the same quality without breakage of tooling and wear out of the machine.
5. Check punching force and compatibility with the machine.
Every machine provides some specific value for punching force. The punch chosen should comply with the value of punching force capacity in conjunction with the machine. Those causing damage to the machine will be oversized from those providing support for the punch. Always consult the machine manual or seek advice from an industrial supplier before selecting a punch.
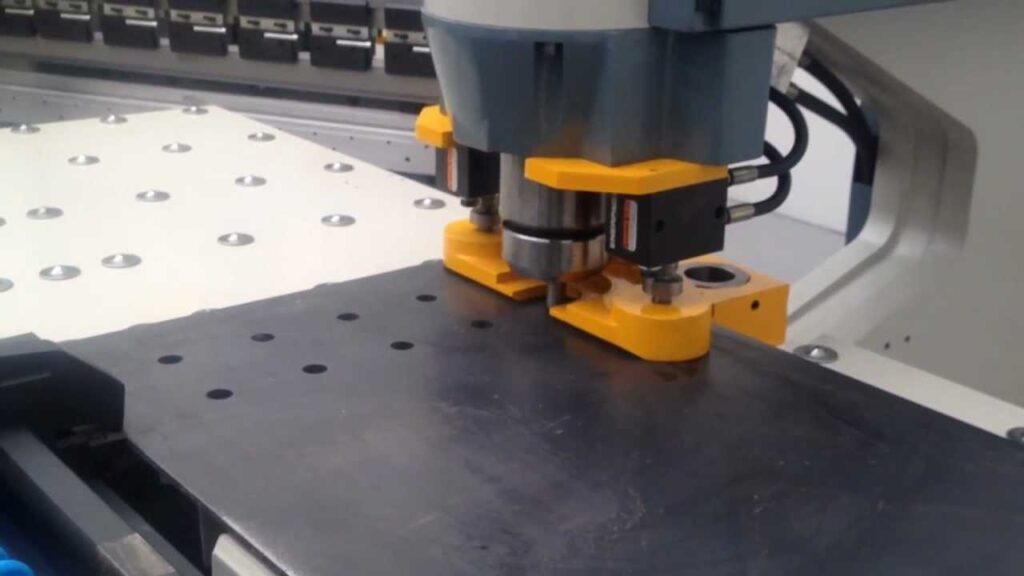
6. Maintain the punch regularly for longevity.
Maintenance itself is one of the practices that helps increase the life of a punch. Included in these basic recommendations will be: lubricating the punch, as a conducting party; proper storing of the punch in a clean, dry, and organized manner to prevent damages; regularly inspecting the punch for wear and replacing those that need to be replaced at that time. Using high-quality punches from a reputable industrial equipment supplier increases durability and reduces downtime further.
7. Balance Cost and Quality
Cheaper punches might be tempting in times of budget constraints, but, really, an investment in higher-quality punches will pay off in the long run. Higher-quality punches give better service, and programs need to replace them less frequently, and thus this indirectly helps lower their overall operating costs.
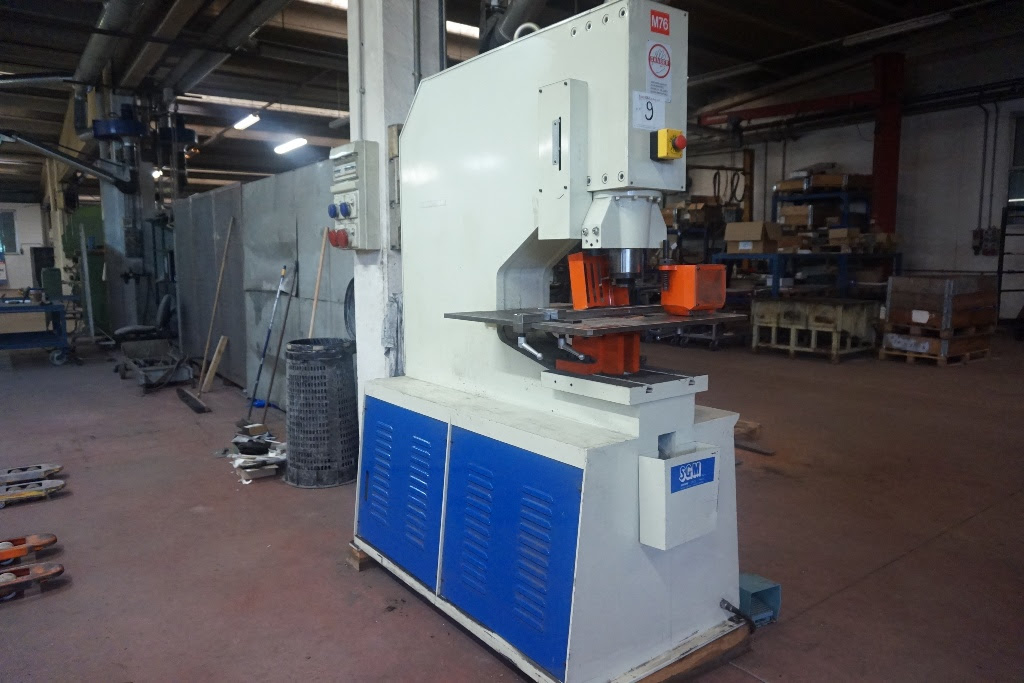
Finding a Reliable Supplier for Punches
To get the best punches for your hydraulic punching machine, collaborate with a trusted industrial equipment supplier. The ideal suppliers provide:
– Durable and high-quality punches.
– Various shapes and sizes of the punch.
– Technical support and product recommendations.
– Competitive pricing with fast delivery.
A reputable supplier gets you the correct punches designed specifically to go with your machine and project requirements.
Selecting the right punch for your hydraulic punching machine significantly impacts efficiency, product quality, and equipment longevity. By considering factors like material type, punch material, shape, die clearance, machine compatibility, and supplier reliability, you can make an informed decision that benefits your operations.
For businesses in the UAE seeking a dependable industrial equipment supplier, Rockwood Workshop Machines offers top-quality hydraulic punching machines and accessories. Choosing the right supplier ensures you get the best tools to optimize efficiency and enhance performance in your metalworking operations.
To read more, click here: Fastener Insertion Machines: Understanding the Process, Technology, and Benefits