Today’s manufacturing is all about being fast and reliable. Many workshop tools have become the game-changers for the production processes-these include fastener insertion machines. These special machines can quickly and repeatably automate the insertion of fasteners like rivets, screws, nuts, and studs into various components to boost production speed, consistency, and quality. The further examination will unveil how these machines operate, what technology they rely on, and a few important advantages of their presence in today’s manufacturing environment.
The Evolution of Fastener Technology
Before automated solutions, fastener insertion was primarily a manual process—time-consuming, labor-intensive, and prone to human error. For the majority of history, workers have manually positioned each fastener-an incredibly inefficient and tedious task-rather than doing it blindly, which ultimately led to inconsistencies, uneven distributions, and low quality. As manufacturing grew, new, more efficient solutions needed to be developed.
Enter the fastener insertion machines, designed to automate this integral assembly operation. These technically advanced workshop tools have traveled the whole distance from simple mechanical devices to highly sophisticated computer-controlled systems capable of inserting a large variety of fasteners with a remarkable degree of accuracy.
Understanding How Fastener Insertion Machines Operate
The automation of fastener insertion generally occurs in the following stages:
1. Feeding System
Contemporary fastener insertion machines commence with an automated feeding mechanism. Fasteners are placed into a hopper or magazine and then oriented correctly for entry into the insertion process. Advanced machines can handle multiple fastener types and sizes, with quick-change systems allowing for rapid production changeovers.
2. Component Positioning
Precise positioning is important for successful fastener insertion. The workpiece is secured on a fixture or conveyor system, often using vision systems or sensors to verify proper alignment. Some advanced machines incorporate robotic arms to manipulate components into the correct position.
3. Insertion Process
The actual insertion varies based on the fastener type:
- For rivets, the machine positions the rivet and applies pressure to deform it
- For self-clinching fasteners, controlled pressure presses the fastener into designated perforations.
- For threaded inserts, the machine applies rotational force to drive the fastener into place
4. Quality Verification
Top-of-the-line fastener insertion machines equipped with quality control systems ensure that the fasteners are correctly inserted. These include sensors that measure insertion depth, applied force, or torque and ensure that each fastener meets the required specifications. Some machines can automatically reject any component that does not have a properly installed fastener.
Advanced Technologies in Modern Fastener Machines
The machines for fastener insertion made today have quite a few modern technologies into play:
Servo Control Systems
In contrast to their dated pneumatic systems, servo-controlled ones boast greater accuracy, programmability, and features. These systems allow real-time adjustments of insertion force and speed to create differing material and fastener requirements.
Vision Systems
Integrated cameras and image processing delegate machine to check on component positioning, fastener orientation, and insertion quality. In this way, substandard insertion would remain undetected.
Industry4.0 Compatibility
Nowadays, connecting fastener insertion machines to networks is something quite fashionable in modern-day workshop tools. Then, it may share information with an execution system for manufacturing, control production in real-time, and enable predictive maintenance and process optimization.
Multi-axis Control
Advances in some special multi-axis systems provide possibilities for inserting complex shapes along with several types of fasteners without the need to reposition parts.
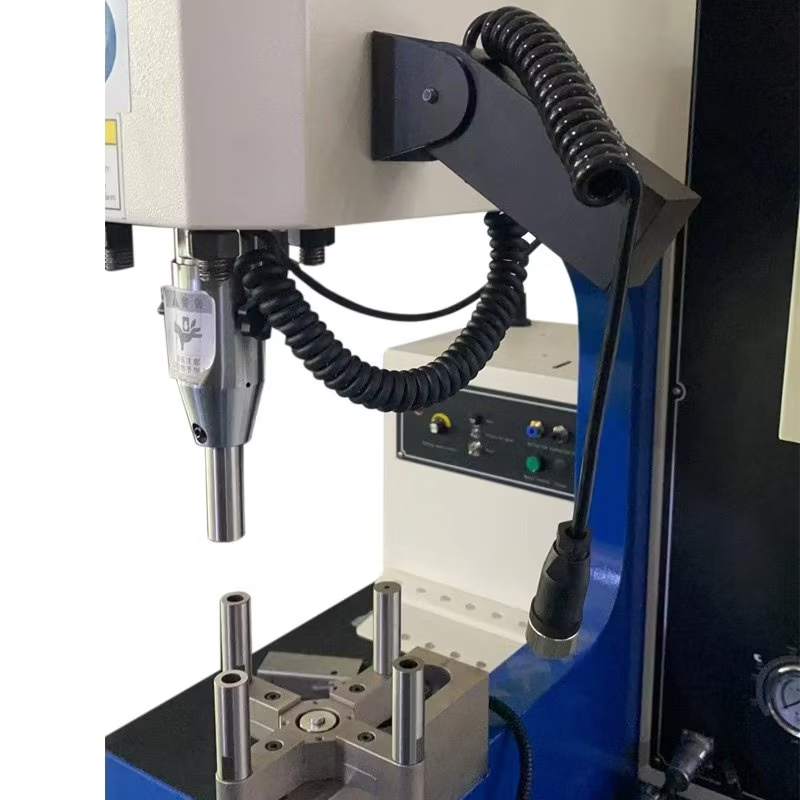
The Business Benefits of Automated Fastener Insertion
Implementing Fastener Insertion Machines delivers several significant advantages:
Increased Productivity
Automated systems can insert fasteners at rates many times faster than manual methods. A machine that can place 30-60 fasteners per minute dramatically outperforms even the most skilled human operator, who might manage 5-10 per minute.
Improved Quality and Consistency
With Fastener Insertion Machines in place, it is now possible to eliminate human variability, resulting in integrity and depth of insertion, orientation, and force application being consistent. This not only reduces the defect rates but also enhances the overall standard of the final product.
Reduced Labor Costs
Workshop machines of this type, while proving to require a huge initial investment, continue to save on labor costs. Such machines often directly replace several manual workstations, requiring only a single operator.
Better Worker Safety
Automated fastener insertion removes employees from repetitive tasks that can contribute to strain injuries. Furthermore, the risks associated with the manual handling of insertion tools and presses would also disappear.
Material Saving
Precision in controlling the insertion reduces waste arising due to erroneously installed fasteners- extremely valuable when the specialized fasteners employed are costly or the components involved are delicate.
Data Collection and Process Improvement
Modern machines collect extensive data at each insertion operation, allowing manufacturers to recognize trends that let them optimize processes and document quality assurance efforts.
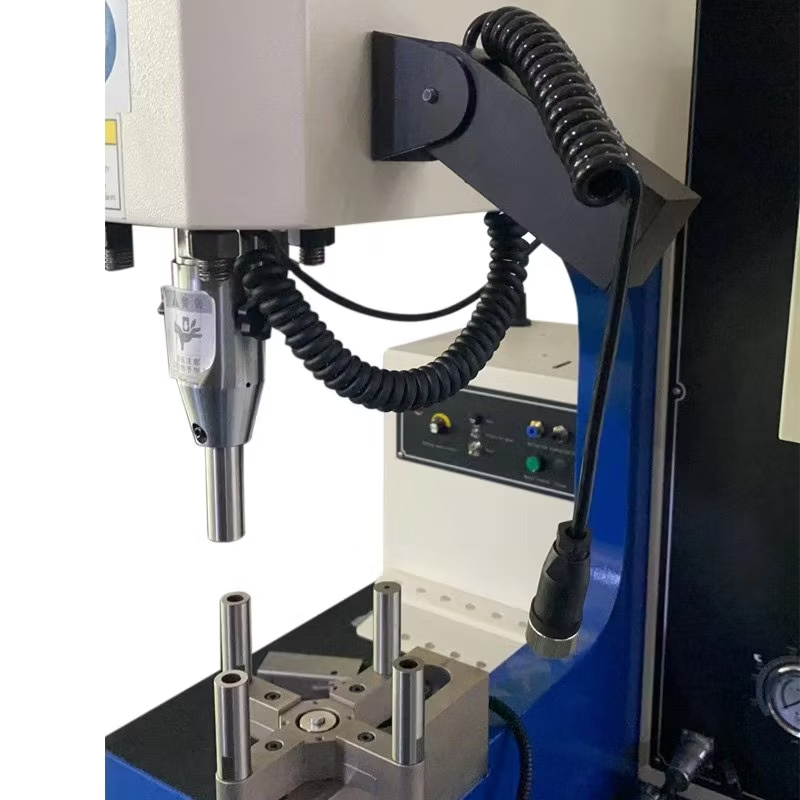
Selecting the Right Fastener Insertion Solution
When considering Fastener Insertion Machines for your operation, several factors deserve attention:
- Production volume – Higher volumes justify more sophisticated automation
- Variety of fasteners – Some machines specialize in specific fastener types, while others offer flexibility
- Component materials – Different materials require specific insertion technologies
- Quality requirements – Critical applications may demand advanced verification systems
- Space constraints – Machines range from compact benchtop units to large automated cells
- Integration needs – Consider how the machine will fit into your existing production flow
The Future of Fastener Insertion Technology
With the ongoing evolution in manufacturing, fastener insertion machines can only get better. Development in the area of artificial intelligence provides scope for smarter quality control; advances in robotic technologies will allow for more flexible handling of advanced components.
For manufacturers that consider investing in fastener insertion machines and other workshop tools of high quality, Rockwood Workshop Machines has a complete range of solutions. Its experts can assist you in assessment regarding the specific requirements you have in mind and propose suitable technology to enhance your fastener insertion operations and returns on investment.
To read more, click here: Why Plate Straightening and CNC Leveling Are Essential for Steel Fabrication