Lathe machines are one of the most versatile machines in the production and fabrication industries. These machines can do various operations, from cutting, sanding, knurling, deformation, drilling, and more. However, one of the most common problems experienced by machinists and operators is chatter and vibration during operation. These oscillations cause a range of problems, including poor surface finish, decreased tool life, and machine damage over time.
Understanding the causes of chatter and knowing how to eliminate it is a productivity consideration for any operator and an essential consideration for high-throughput production lathe work. No matter if you are a hobbyist, running a small volume job shop, or a high-volume production shop, eliminating vibration will help you produce the best results from your lathe machine.
This blog post will outline some of the best practical ways to identify, respectively address, and eliminate chatter and vibration with your lathe machine. We will also look at how a reputable industrial equipment supplier in the UAE, such as Rockwood Workshop Machines, can assist your machining operations with reliable tools and equipment.
What is Chatter in a Lathe Machine?
Chatter is a type of sustained vibration that occurs during machining. It makes a loud noise and produces a surface with a wavy or rippled pattern. Chatter and vibration are not random, but are the result of the interaction between the cutting tool and the workpiece; other causes include poor machine setup, loose components, or incorrect cutting conditions.
Common Effects of Chatter and Vibration:
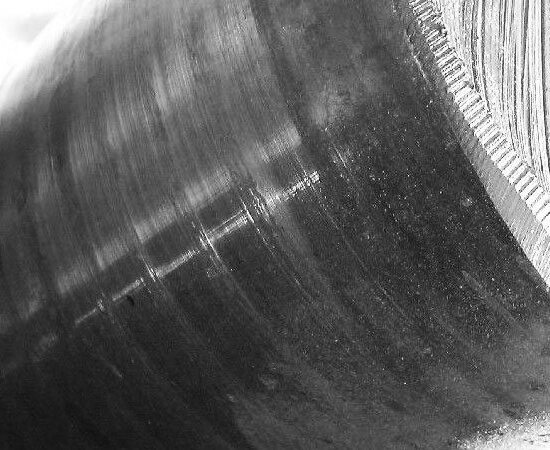
- Poor surface finish and dimensional inaccuracy
- Premature tool wear or breakage
- Increased wear and tear on the machine
- Reduced production efficiency and part quality
Step-by-Step Guide to Eliminate Chatter and Vibration
1. Inspect and Maintain Machine Rigidity
Chatter often begins with a lack of machine rigidity. Over time, even high-quality lathe machines can develop play in critical components due to wear.
- Tighten all bolts and joints, especially around the cross slide, carriage, and tailstock.
- Replace worn bearings or lead screws to eliminate backlash.
- Ensure that your lathe is properly leveled and secured to a solid foundation.
- A poorly maintained or misaligned machine will always be more susceptible to vibration.
2. Use the Right Tooling
Tool selection plays a significant role in minimizing vibration. Improper tooling can amplify cutting forces and destabilize the machining process.
- Use shorter tools to reduce tool overhang. The longer the tool, the greater the chance of vibration.
- Choose cutting tools with the correct geometry, especially rake angle and nose radius.
- Regularly sharpen or replace dull tools, which can create excess friction and chatter.
- For high-performance needs, consider investing in anti-vibration tool holders or dampened boring bars.
3. Secure the Workpiece Properly
A poorly clamped or unsupported workpiece can easily vibrate under cutting pressure.
- Use a steady rest or follow rest for long, slender workpieces.
- Reduce overhang by adjusting the setup for the shortest possible length-to-diameter ratio.
- Use soft jaws or custom fixtures for delicate or irregular-shaped parts.
Ensuring the workpiece is firmly supported reduces the potential for movement during cutting, which in turn reduces chatter.
4. Adjust Cutting Parameters
Often, tweaking your cutting speeds and feeds can help eliminate vibration.
- Reduce spindle speed when chatter occurs at high RPMs.
- Increase feed rate slightly to stabilize chip formation.
- Avoid excessively deep cuts. Instead, make multiple shallow passes.
Many lathe machines come with built-in charts to guide these settings based on material type and tooling. However, fine-tuning based on actual cutting behavior is sometimes necessary.
5. Improve the Machine Base and Setup
The foundation your lathe sits on matters more than many realize. If your machine is on an unstable or uneven surface, vibration will be amplified.
- Place your lathe on a level concrete floor or install vibration-dampening pads.
- Make sure the machine sits evenly with all feet firmly touching the ground, and use shims if needed.
- If your machine is mobile, consider locking it in place during operation.
This step is particularly important for high-speed operations or precision work.
6. Balance Rotating Components
Imbalance in the spindle or chuck is a common source of vibration, especially at high rotational speeds.
- Check for runout in your chuck or spindle using a dial indicator.
- Balance your chuck or workholding fixture if you notice uneven rotation.
- Clean all contact surfaces before mounting a workpiece to avoid misalignment.
Even small imbalances can make a big difference at higher RPMs.
7. Consider Aftermarket Solutions
If you’ve already optimized tooling and parameters but still face issues, several vibration-dampening solutions are available:
- Tuned mass dampers for long or slender tools
- Vibration-absorbing tool holders
- Bar holders with internal dampening systems
While these can be an investment, they are often worth it for high-precision or high-value workpieces.
Final Thoughts: Precision Starts with Prevention
Chatter and vibration can severely impact your machining quality, productivity, and equipment lifespan. By taking a proactive approach—through regular maintenance, thoughtful setup, proper tooling, and stable foundations—you can ensure your lathe machines run smoother and deliver consistently better results.
At Rockwood Workshop Machines, we specialize in delivering premium industrial machinery designed specifically for machinists and workshops across the region. As a trusted industrial equipment supplier in the UAE, we understand the demands of modern manufacturing. That’s why we offer a complete range of lathe machines, accessories, and precision tooling to help eliminate chatter and enhance performance.
Whether you are setting up a new machine shop or upgrading your existing equipment, our experienced team is here to guide you with expert advice and reliable support.
To read more, click here: Top 7 Features to Look for in an Ironworker Machine for Precision Metalwork