Tapping in hard-to-reach areas is a common challenge in the manufacturing world. As designs grow more complex in industries like aerospace, automotive, and electronics, manufacturers often encounter components with intricate geometries. This makes the process of creating internal threads in confined spaces a demanding task. Fortunately, tapping equipment and workshop machinery dealers are coming up with smart solutions to address these hurdles. Let’s identify the main challenges and develop strategies to overcome them.
Common Challenges in Hard-to-Reach Tapping
- Limited Access
Many components, such as engine blocks or electronic housings, feature threading points positioned deep within their structure, making it difficult to access them with standard tapping machines and frequently necessitating creative setups. - Maintaining Precision
Getting the threads right is critical, especially in tight space. Even a tiny error in alignment can cause cross-threading, which can damage the part’s durability and performance. - Tool Wear and Damage
Working in confined areas puts extra strain on tapping tools. Issues such as insufficient cooling can result in overheating, which may cause tools to wear out prematurely or even break. - Challenging Materials
Some hard-to-reach areas involve tough-to-machine materials like stainless steel, titanium, or composites. These materials need specialized tools and techniques to ensure a smooth operation. - Skilled Labor Dependency
Tapping in tight space typically needs expertise and careful oversight, which can extend the time needed for production and increase the possibility of errors. - Machine Limitations
Older or less flexible tapping machines may not be designed to handle unconventional setups. Fixed spindle orientations and limited range make it difficult to tackle intricate geometries.
Smart Solutions for Better Tapping
Thankfully, machines and technology today make tapping, even in hard-to-reach areas, relatively easy to do. These are some current recommendations:
- Adaptable Tapping Machines
Today’s tapping machines provide multi-axis flexibility, enabling an operator to set the tool to work in odd positions. The precise setting will reduce the amount of errors while improving efficiency. - Improved Tapping Tools
A new generation of boring tools made from super-performance materials containing carbide and which have a wear-resistant coating finished survive the toughest conditions and produce better results. - Portable Machines for Tight Spaces
A compact portable tapping machine is perfect for jobs in confined areas. It can be brought and remodeled at a job site for maintenance or repairs. - Increased Performance-Through New Coolants
After tool life, another consideration in smooth operation is cooling. Latest systems, like through-tool coolant or high-pressure cooling, help keep the tool cool and effective, even when threading deep or narrow spaces. - CNC Integration
CNC (Computer Numerical Control) technology has revolutionized tapping. CNC machines deliver high precision and consistency, making them invaluable for intricate jobs. Automation may reduce the demand for skilled labor in certain manufacturing processes. - Articulating Arms and Extensions
For more complicated geometries, accessories such as articulating arms and tool extensions have a big role to play. This helps operators work around the obstruction and to reach areas that cannot be reached with standard machines. - Real-Time Monitoring
Advanced tapping machines now feature real-time monitoring systems that track torque, speed, and tool wear. This data helps operators fine-tune the process, reducing downtime and tool damage.
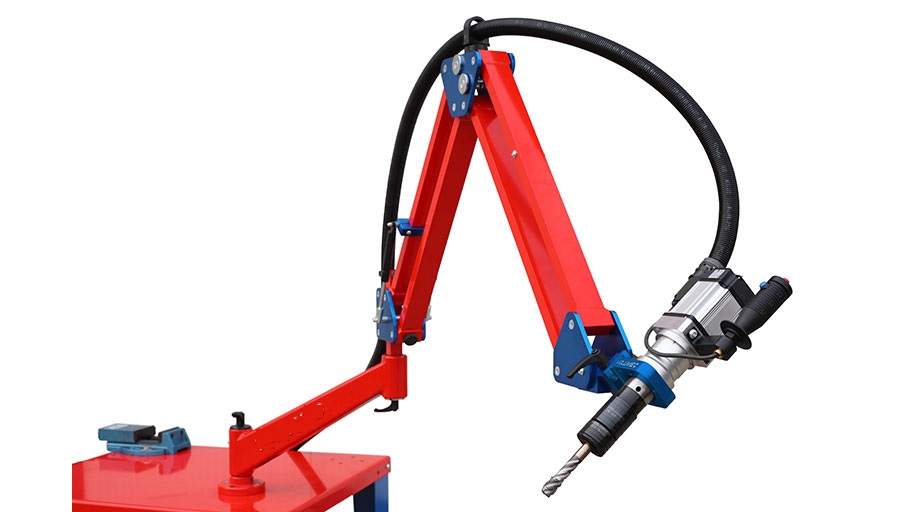
Picking the Right Tapping Equipment
For successful tapping operations, selection of the correct equipment is required. The factors to consider include-
- Flexibility of Machines: Ensure that the machining machines are multi-axis types involving setups.
- Durable Tools: Quality tapping tooling material with high-performance coating increases life.
- Support Service: Work with workshop machinery dealers that provide training, maintenance, and support.
- Customizability: Some projects might require machines or tools specially made for the job.
The Role of Workshop Machinery Dealers
Workshop machinery dealers are key players in solving tapping challenges. They provide manufacturers with cutting-edge technology and customized solutions. A good dealer will provide:
- Guidance on selecting the best tools and machines.
- Training and demonstrations to maximize performance.
- Maintenance services to keep machines running smoothly.
Threading hard-to-reach areas becomes manageable with the right method and the correct equipment. Manufacturers can now confidently tackle the most complex projects thanks to significant advancements in tapping machines, tools, and techniques. Partnering with experienced workshop machinery dealers like Rockwood Workshop Machines ensures access to cutting-edge solutions and expert support. With the right tools and strategies, you can improve precision, efficiency, and reliability in your tapping operations.
To read more, Click here: The Impact of Heavy-Duty Horizontal Lathes on Modern Manufacturing