In the industry of metal fabrication, precision is everything. Whether you are punching, shearing, notching, or bending, making sure you have the right equipment in your shop is essential to efficiently achieving a high-end product. The ironworker machine stands out as a highly versatile and indispensable tool in any fabrication shop.
Ironworker machines are built to perform a broad range of metalworking functions, making them a reliable choice for professionals in the industry. But with so many options and models, it can be difficult to choose the right ironworker.
To help you choose the best option, I have compiled a list of the top 7 features to look for in an ironworker machine when precision metalwork is the goal, whether you are working on an upgrade for equipment or starting a brand new operation. This list will help ensure you are making a tough but smart investment.
1. Hydraulic Power for Smooth Operation
When considering ironworker machines, one of the first things you will want to be mindful of is what kind of power plant system they have. Generally, hydraulic ironworker machines are preferred because of the smooth and consistent nature of hydraulic systems. Hydraulic machines typically are quieter, have less wear and tear, and have greater control over pressure and movement compared to mechanical systems.
This means cleaner cuts, more accurate punching, and fewer operator errors. Hydraulic systems are also more adaptable to different types of materials and thicknesses, which makes them a good choice for shops that do all kinds of work.
If precision and repeatability are important to you, you will want to choose a hydraulic model.
2. Multi-Station Capability
The advantage of using an ironworker machine is being able to perform multiple tasks on one platform. The best machines offer several integrated workstations—typically including punching, angle shearing, flat bar shearing, notching, and sometimes even bending.
This all-in-one functionality allows you to switch between operations without having to move materials between machines, saving both time and space. It also means less clutter on your shop floor and better workflow efficiency.
When evaluating machines, make sure each station is well-positioned and easy to operate. Versatility is great, but it only pays off if the layout is user-friendly and intuitive.
3. Digital Controls for Precision and Repeatability
Modern fabrication demands precision, and having digital controls can significantly improve the accuracy of your work. High-quality ironworker machines now come with digital readouts or even CNC compatibility, allowing for precise control over dimensions and positioning.
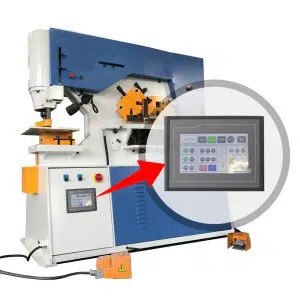
Digital systems help reduce setup time, eliminate guesswork, and improve the consistency of your results, especially important when handling large production runs or intricate jobs. Some machines even allow you to store frequently used settings, saving time on repeat tasks.
Whether you’re punching a hundred identical holes or making angled cuts for a custom project, digital control gives you the accuracy and efficiency you need.
4. Solid Build Quality That Lasts
Metal fabrication is tough on equipment, and your ironworker machine needs to be able to handle the pressure—literally. That means looking for a unit with a heavy-duty frame made from reinforced steel, high-quality welds, and durable components.
A sturdy frame reduces vibration and improves cutting precision, while hardened tooling—like punches and blades—helps extend the machine’s lifespan. Look for machines that are rated for the type of workload you expect, and don’t compromise on build quality to save a few bucks.
A well-built ironworker is a long-term investment that will serve your shop for years with minimal maintenance.
5. Strong Safety Features to Protect Operators
Ironworker machines are powerful, and like any powerful equipment, they require careful handling. Good machines come with built-in safety features like two-hand control systems, foot pedal operations, safety guards, and emergency stop buttons to reduce the risk of accidents.
But safety is about more than just hardware. A thoughtfully designed machine should also be comfortable and easy to use. An ergonomic layout ensures that controls are easy to reach and that operators can work efficiently without excessive strain or fatigue.
Safety should always be a top priority in your shop, not just to protect your team, but also to ensure more efficient workflows and minimize disruptions.
6. Quick Tool Change Systems for Time Efficiency
If your workshop handles a variety of projects throughout the day, you know how time-consuming it can be to constantly switch out tools. That’s why many modern ironworker machines come equipped with rapid tool-switching systems.
These systems allow you to switch from punching to shearing—or from flat bar to angle iron cutting—in a matter of minutes, rather than spending valuable time on lengthy setup procedures.
Some models also offer built-in storage for tools, which helps keep everything organized and within reach. When you’re juggling multiple jobs in a busy shop, features like this can boost your productivity.
7. Maintenance Access and After-Sales Support
Even the most rugged machine will need maintenance from time to time. That’s why it’s crucial to choose an ironworker that’s easy to service. Look for models with accessible components, removable panels, and easy-to-follow maintenance guidelines
Just as important is your relationship with your equipment supplier. Consistent customer service, availability of replacement parts, and dependable technical support can make a huge difference in minimizing downtime.
Before making your purchase, ask questions about service response times, warranty coverage, and the availability of replacement tooling. Being able to access expert help promptly by phone ensures greater confidence and continuity.
Final Thoughts
Choosing the right ironworker machine isn’t just about power—it’s about precision, safety, speed, and long-term value. From hydraulic systems and digital controls to multi-station functionality and quick tool changes, the features you prioritize will directly impact your productivity and results.
Equally critical to the equipment is selecting the right supplier to back it. If you’re looking for a trusted industrial equipment supplier in the UAE, Rockwood Workshop Machines offers a wide selection of ironworker machines designed for professional metalworkers. With durable construction, advanced features, and strong after-sales support, Rockwood is a solid partner in helping you elevate your fabrication capabilities.
To read more, click here: How AI and Automation Are Transforming the Way We Choose Workshop Equipment